Laser Cleaning: A Powerful Tool with Safety in Mind
Laser cleaning is an innovative, environmentally friendly, non-contact method of removing contaminants, rust, or coatings from surfaces. Laser cleaning uses high-energy focused laser beams to clean the objects without damaging the base material. The laser vaporizes or breaks down unwanted layers through precise control of the laser energy.
This technology has found applications across industries like manufacturing, aerospace, and automotive for its precision, efficiency, and minimal waste production compared to traditional cleaning methods. Traditional techniques like chemical and abrasive cleaning can be harmful to the environment and may damage delicate surfaces.
For these reasons and more, the use of laser cleaning has significantly increased in recent years. Laser cleaning offers a safer, non-contact alternative with minimal waste production, making it an especially attractive alternative. Its ability to clean surfaces without requiring chemicals or water has also contributed to its rapid adoption, particularly as environmental regulations become stricter.
Though laser cleaning has garnered approval from environmental regulations, it now must come face to face with the safety regulations. As with any powerful tool, safety is a crucial consideration. The risks associated with laser operationsāsuch as high-intensity beams, reflections, and exposure to hazardous materialsāunderscore the importance of robust safety protocols and regulations to prevent accidents.
Understanding the Laser Hazards
Laser cleaning uses high-energy beams, often in the infrared spectrum, to vaporize surface contaminants. This process poses several potential risks such as eye damage, skin burns, and other material hazards.
Direct or reflected laser beams can cause serious eye injuries, including retinal burns or even partial or total loss of vision.
High-power laser radiation can damage skin tissue if operators are exposed to direct beams or even reflections.
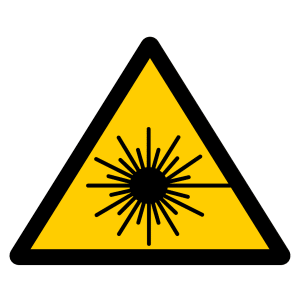
Ablated materials from the laser cleaning process can be hazardous, releasing toxic fumes or particulates during the operations.
In addition to physical risks, improper laser handling can also damage equipment or cause unintended environmental harm.
The Importance of Laser Safety
Given the risks, laser safety in the workplace is non-negotiable. Several organizations and regulatory bodies, such as the Occupational Safety and Health Administration (OSHA) and the International Electrotechnical Commission (IEC), provide guidelines for laser safety. One of the most widely recognized standards is EN 60825, formally titled āSafety of Laser Productsā.
Standard EN 60825 covers safety requirements for laser equipment, classification of lasers based on their hazard levels, and guidelines for safe use in various environments. It is widely used across Europe to ensure the safety of workers and the general public when lasers are in operation, much like ANSI Z136 in the United States.
Key safety measures include:
- Laser Safety Training: All personnel operating or working near laser cleaning equipment should undergo comprehensive training on the safe use of lasers in addition to training in the operation of laser machinery.
- Personal Protective Equipment (PPE): Personnel must wear laser safety goggles or eyewear to protect their eyes from direct or reflected laser beams, as well as protective clothing to avoid burns.
- Controlled Work Areas: Laser cleaning should be performed in designated areas with appropriate signage and enclosures to prevent accidental exposure to laser beams. For more complex arrangements, integrated interlock systems can help to achieve safety when PPE and laser guards are not enough.
- Proper Ventilation: When removing hazardous materials like paint or rust, ventilation systems should be in place to capture fumes and particulates, protecting workers from inhaling toxic substances.
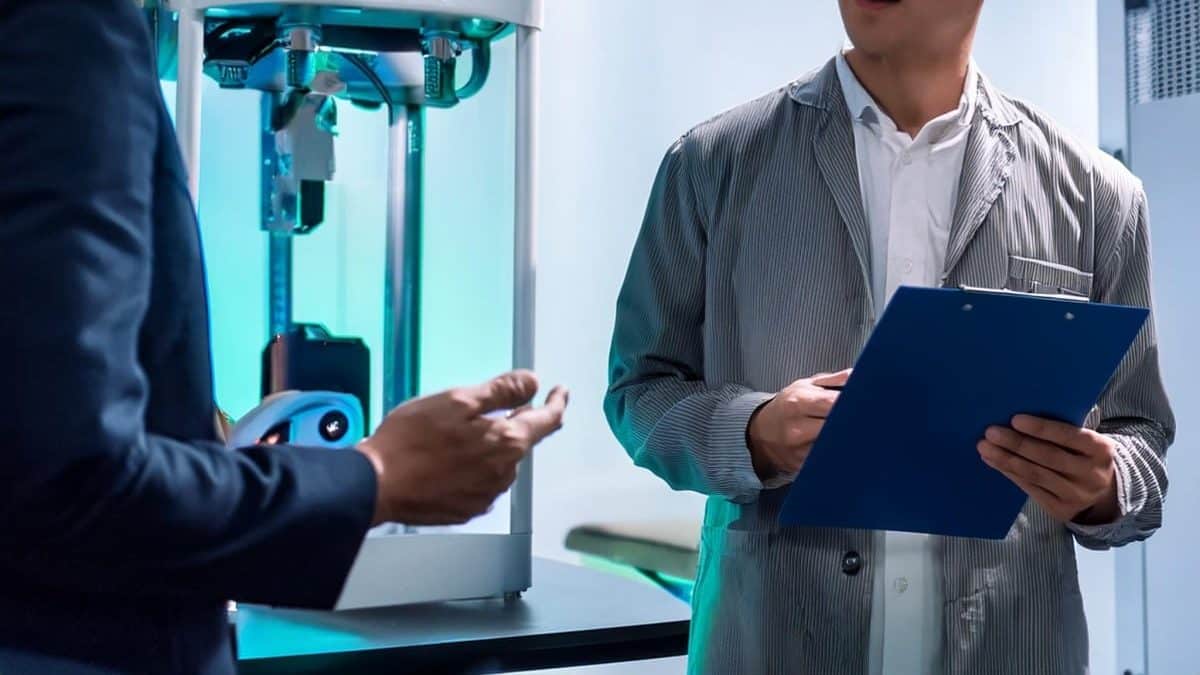
Laser Accident Statistics: A Wake-Up Call
Accidents involving lasers are not uncommon, particularly when safety protocols are neglected.
While specific UK laser accident statistics are harder to come by in public sources, Rockwell Laser Industries previously maintained a Laser Accident Database that included incidents from around the world. The database, though no longer active, suggests that incidents involving misalignment or failure to use appropriate protective gear, such as eyewear, are frequent causes of injuries.ā
According to the Laser Institute of America, thousands of laser-related injuries occur annually in the U.S., with nearly 60% affecting the eyes.
Many of these accidents can and will be prevented with proper safety training and compliance with safety regulations.
Compliance with Safety Standards
Strict adherence to laser safety standards, such as OSHAās guidelines on laser safety and EN 60825, is crucial in reducing accidents.
Regulations often require employers to implement engineering controls, such as laser enclosures and interlock system mechanisms to safeguard workers and the environment from stray laser radiation. Where engineering controls are not enough, administrative controls may be established which include operational procedures and emergency protocols.
In addition, regular risk assessments and inspections of laser equipment should be carried out by qualified professionals. In most countries, a Laser Safety Officer (LSO) is required and is responsible for overseeing the safe use of lasers within the workplace. Their primary duties involve ensuring that all laser systems are operated according to established safety standards and regulations to prevent accidents or injuries.
Employers who fail to comply with these regulations not only risk worker injuries but also face penalties, fines and legal consequences.
The Lasermet Solution
As early as 2011, Lasermet’s certified laser blocking curtains have been used by the Acropolis Museum in Athens to enable laser restoration work to be carried out on ancient sculptures.
Lasermetās laser blocking curtains (or modular curtain pods) are able to be quickly set up and transported to set up a laser work area indoors or outdoors. This is especially useful when the objects being cleaned are too big, too heavy, or too valuable to be moved around.
Lasermetās own specially developed Laser Blocking Curtains come in a variety of material options and are customisable to virtually any size.
Browse Lasermetās offerings
Safety First in Laser Cleaning
Laser cleaning is a game-changer for many industries, offering a cleaner, more precise method of removing surface contaminants. However, the power of laser technology requires equal amounts of respect and caution. By implementing comprehensive safety measures and complying with industry regulations, companies can enjoy the benefits of laser cleaning while protecting their workers from harm.
The statistics are clear: when safety is ignored, accidents happen. But with the proper training, equipment, and adherence to safety standards, laser cleaning can be a safe and highly effective solution for modern industries.
Need a solution? Contact Lasermet today.
Lasermet provide a full range of laser enclosure cabins and laser interlock system equipment which can be interconnected to provide a complete turnkey solution. We also supply training, audits, and consultancy services covering all aspects of laser safety. Full support, design, and installation is available from Lasermet.
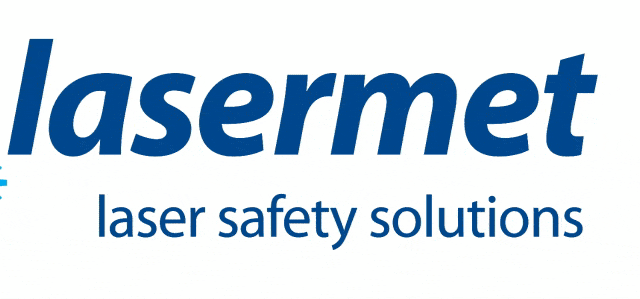